Labels Dulux
-
Sectors
chemistry
-
Product
adhesive label
-
Technology
digital print HP Indigo
-
Base
Paper

Production of labels for paint cans and buckets is one of the most difficult tasks for a printing house. Most paint containers, unlike other packages, have more than one adhesive labels. For example, a Dulux paint bucket has at least four of them, each with a specific function.
The first, biggest label is decorative. Its main task is to attract the customer’s attention so that they see a specific product. Other than that, it includes: the manufacturer’s logo, product name and description.
Sometimes, a paint manufacturer decides to change the product’s graphic design when there are still older versions of packages in warehouses. It necessitates designing a new label for cans or buckets, one which will not only perform all the above functions, but also thoroughly cover the previously fixed older version. In such a case, opaque labels are used.
The second label includes the barcode, scanned at the store checkout. The code contain information about the size of the package, and the paint type and color. Therefore, it also has to be consistent with the label depicting the color, as described below.
Another label is put on the can lid or bucket cover. It contains basic information about the paint brand and type. It also quite often includes information on ongoing promotional offers and other messages the manufacturer wants to convey to the customer. This type of can labels have to be legible so that they perform their function even when the paint containers are on the bottom shelves at a store with construction materials.
The last label might be the most important and doubtlessly the most difficult to make. It is the so-called color chip. It contains the most essential information from the customer’s point of view, what a wall coated with the paint will look like. And this, unfortunately, is where it gets tricky…
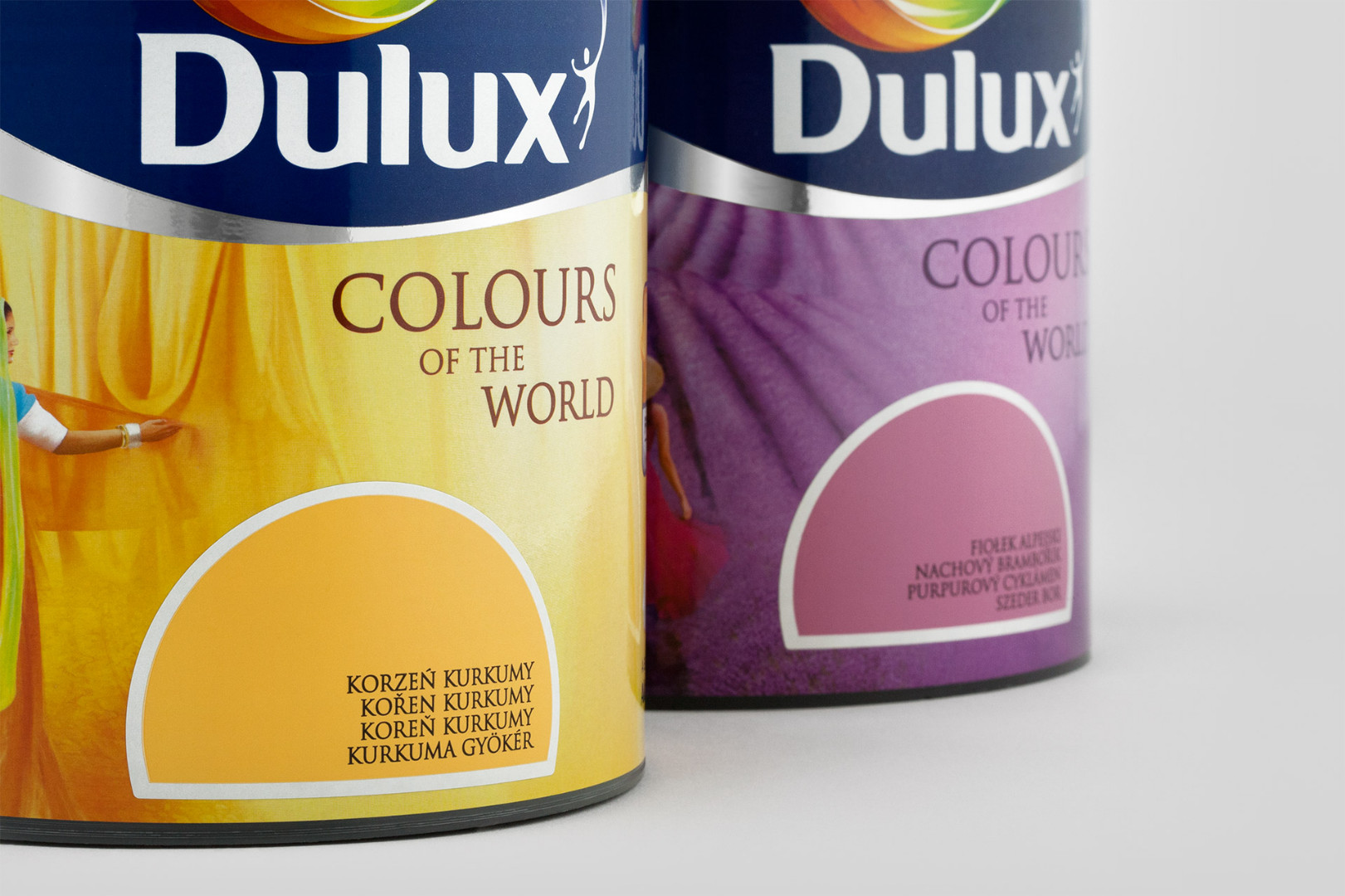
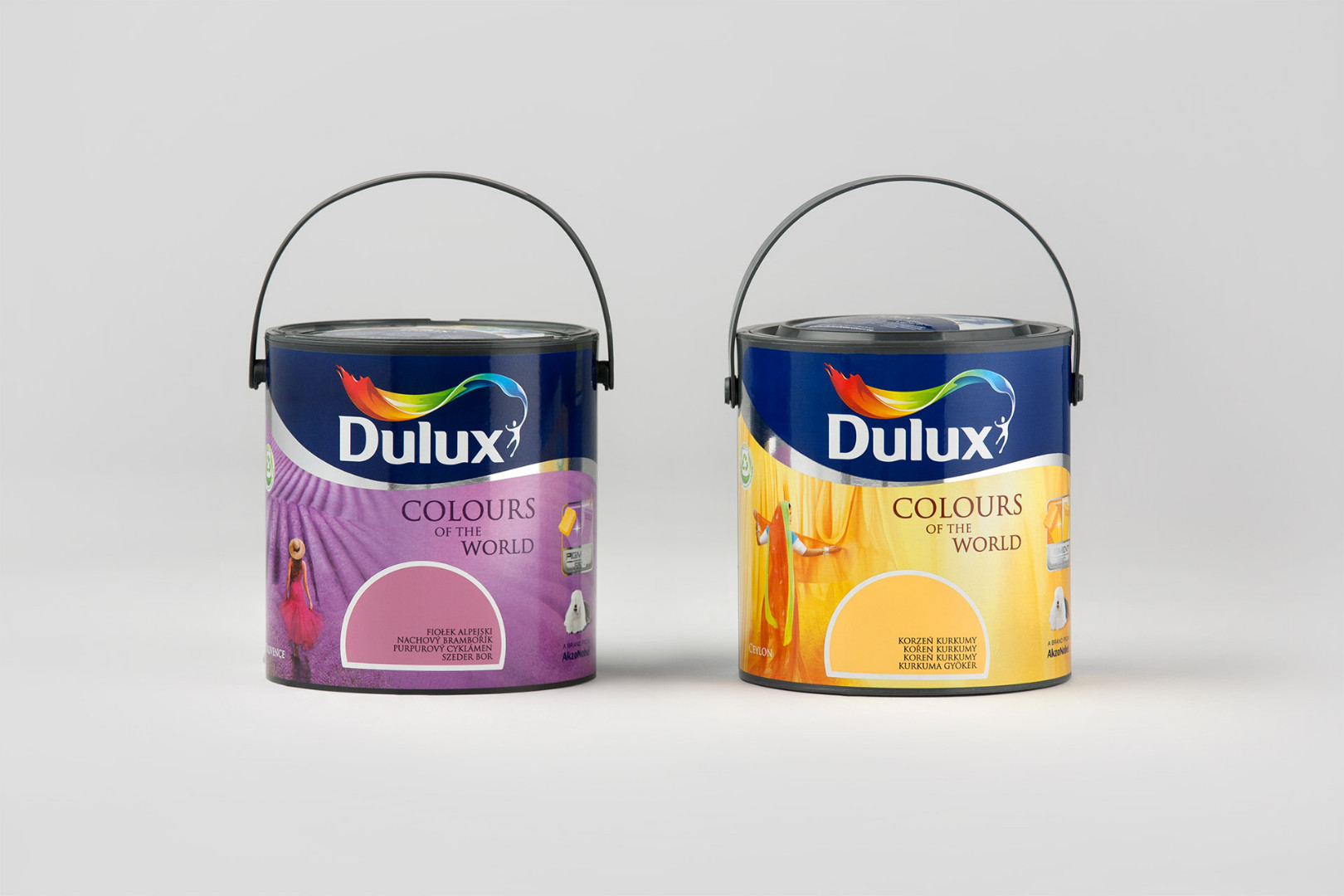
In order for the customer to get reliable information and not be disappointed with a painted surface being significantly different from what they saw on the package, the color reproduced on the label needs to be nearly 100 percent consistent with the color of the paint in the can.
Achieving this outcome is not easy. First comes a stage of selecting the appropriate color before printing even begins (so-called color matching). But that is not enough – it is also necessary to perform spectrophotometric control during the production, a measurement of the amount and quality of reflected light, conducted using special equipment.
The precision of color selection and its consistency with what is actually in the can are extremely important, also from the manufacturer’s point of view: most cases of complaints and returns of paint by retail customers are caused by none other than inconsistency of a coated wall’s color with that on the label. Indeed, it is difficult to hold it against a customer who wanted to have a specific color of their mantel wall, and the end result looks completely different…
In order to minimize the risk of such situations, it is worth going with the HP Indigo printing technology. It is a bit more expensive than such techniques as flexography or offset, but it ensures one hundred percent reproducible color in every subsequent batch of labels or packages.